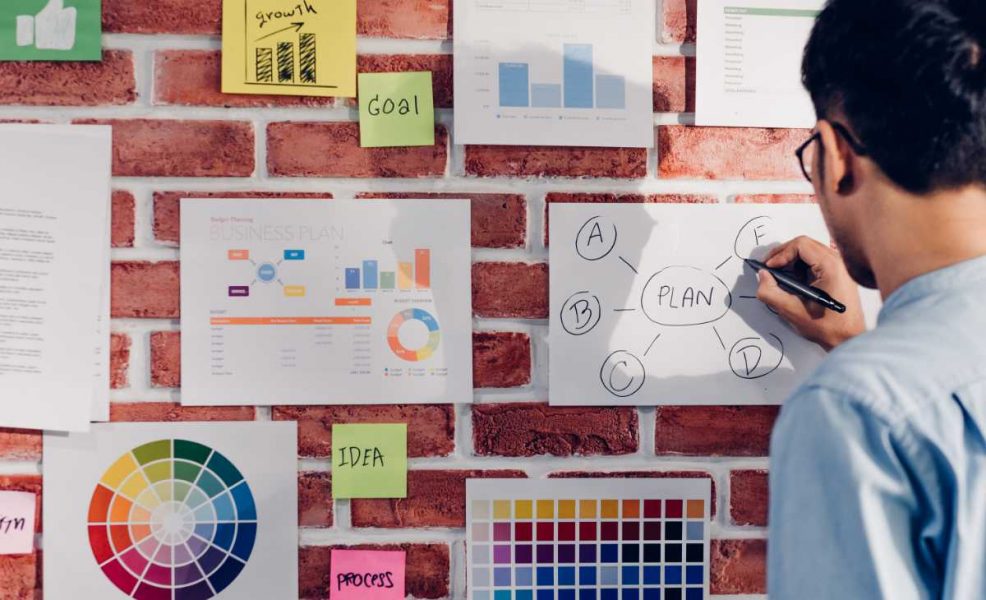
Evaluating your business practices is essential for anyone who wants to stand out in the market. Companies must seek operational effectiveness, motivate employees and increase their competitiveness. The challenge is even more significant in the late globalization of the southern hemisphere.
One of the main continuous improvement techniques is the PDCA Cycle, a worldwide management method. The tool is ideal for controlling and continuously improving processes, and the acronym reveals four specific steps:
- Plan
- Do
- Check
- Act
The objective of the PDCA Cycle is to understand, on the one hand, how a failure arises and, on the other hand, how it can be solved. When an improvement opportunity is identified, it is possible to define actions to promote changes.
Therefore, from the PDCA it is possible to extract solutions to problems and assist in the execution of strategic planning. It is widely used in quality management but can be easily applied in any organizational area.
This article will unravel the PDCA Cycle and its four stages.
Plan
In this first step of the cycle, we work on three levels:
- Identification of factors that influence the problem
- What are the causes of the problem
- What objectives and goals do you want to achieve.
The first step is to investigate your organization’s current situation. From this overview, understand the nature of the problem to be solved in depth. With this, identify possible solutions.
And it is here that the Action Plan is born, which entitles the stage.
Tip: A handy tool in this step is 5W2H.
How to plan the PDCA Cycle
The planning stage of the PDCA Cycle is divided into 4 phases:
1. Identification of the problem (macro)
With the team, identify the problem or opportunity for improvement in your organization.
Indicated actions:
- Search your history
- View the losses caused
- Set a deadline to resolve
Inputs: To have a more objective view, use reports, data, graphs, and photos.
Tip: With the inputs in hand, Brainstorming is a good tool for this step.
2. Unravel the problem (micro)
This may be the most time-consuming step in the PDCA Cycle.
At this stage, the problem must be unraveled in depth. Indicated actions:
- Identify characteristics of the problem
- Describe how and where it happens
- What areas or functions are involved
Tip: A tool often used at this stage is the Pareto Analysis.
When these actions are completed, it will be possible to:
- Estimate a budget needed to solve the problem
- Define the improvement objective and the goal to be achieved
3. Problem analysis
This step is a consequence of the previous one. Here, the problem’s hypothesis is raised until the root cause is reached. Based on the data collected, keep these actions in mind:
- Identify its various causes
- Arrange them in order of importance
- Select probable or unlikely causes
Tip: To help in this step, the Ishikawa Diagram or the 5 Whys tools are used.
4. Action plan
One of the first phase’s most essential steps is the time to plan. Briefly, here you will define what actions will be taken to solve the problem.
Tools such as 5W2H or Action Plan can be used to guide the development of the stage. Suggested actions:
- Describe clearly and objectively what needs to be done
- Define who will be responsible
- Establish completion dates for each task
Do (Execute)
It’s time to make it happen. It indicates putting into practice the execution of the planned actions and recording all the results, whether good or bad.
Here are five steps that can help you better organize this stage:
- Train the method and those involved
- Implement the improvements
- Collect data that makes sense
- Measure execution progress
- Document results obtained, problems, unexpected observations, lessons learned, and knowledge gained
Make sure that there are no deviations from the Action Plan. If it is impossible to execute what was planned, go back to the first step (Plan) to analyze the reasons.
The Do (Execute) step of the PDCA Cycle is a testing phase. The reason? It verifies what is working and needs to be adjusted in the planning.
Check
In this stage, the progress of the planning and the actions carried out is verified. In addition, an analysis of the results obtained so far with the changes made is carried out.
It must be done only at the end of the actions. Does it make sense to check what hasn’t even ended yet? An alternative would be to develop the check in the first step in the Action Plan.
It is vital at this point to compare the before and after. In addition, assess whether this improvement was successfully achieved. If the results do not meet expectations, it is recommended to return to the initial PDCA phase.
Tip: For analysis and verification of results, there are several relevant tools:
- Pareto’s chart
- Histograms
- Execution charts
- Scatter charts
- Control charts
- Radar charts
See seven quality control tools (Flow Chart, Check Sheet, Pareto Chart, Fishbone Diagram, Scatter Diagram, Histogram, and the Control Charts) explained in this video:
Act (Action)
The last PDCA Cycle step is to reflect on the mistakes and the path to follow from now on. In particular, there are two possibilities:
1. Standardize the improvement
If the proposed objective has been achieved, standardize the improvement. For it to be maintained, it is essential to establish a measurement and monitoring mechanism. In addition, those involved in the change must be trained and educated.
Tip: For performance monitoring, rely on tools such as the run or control charts.
2. Adapt the improvement
If the objective has not been reached or can be more satisfactory, the PDCA Cycle can be rerun.
Suggested actions:
- Revisit the solutions listed the first time
- Re-analyze the root cause of the problem with different data
- Rethink the work methodology
There is no secret; the way out here is to adapt or remake the action plan.
What are the advantages of using the PDCA cycle?
Simple and resolute. The PDCA Cycle is considered one of the most popular methodologies among quality management approaches. The benefits of using this methodology are several:
- Facilitates decision-making
- Stimulates teamwork
- Promotes continuous improvement and learning
- Precise diagnosis of processes
- Standardization of methods
- More agile, precise, and objective processes
- Improved communication
Seema Aziz, the founder of the high-quality fabrics company Sefam in Pakistan, describes the process of creating a corporate culture of excellence and attention to detail on the Harvard channel:
Conclusion
Want better results? So continuous improvement must be a guideline in your company. With the help of the PDCA Cycle, it becomes a process of organizational culture.
It is a cyclical approach. Therefore, its application continues after each use. By the way, it should be applied as many times as necessary. The quest for improvement never ends.
For those who want to go further, get to know the software used by Unimed, Chinalco, and the Ministry of Agriculture of Brazil. Interact Suite SA is a platform for the digital transformation of corporate governance.
Conquer a high management standard with complete software for your company’s continuous improvement.
Click here to learn more.
Reference:
Interact’s Practical Guide to Quality
Authors:
Aline Betinelli
Advertiser. Communication and Marketing Analyst at Interact Solutions.
Vinícius Flôres
Journalist, Ph.D. in Communication, and martech enthusiast. Communication and Marketing Supervisor at Interact Solutions.